Yup none of the plastic rings that I have installed in Midwest after construction are totally flush. I have had to use deep covers on them. I did also trim the inside of the wall plate to make them flush.
They are thin but not thin enough. The metal ones are thin and have sharp edges. Here in the midwest I used these for keystone speaker posts for the externally mounted on the wall speakers. They are behind them and you do not notice the speaker posts.
If there is good communications between the electrical folks and drywall folks there are no issues. That said helped a friend with his new home and did the metal mudplate prewire there. The house is around 6K sized and there were about 10 drywallers in and out of the house in two days and they did very good work and they were fast. It is understood about doing the pictures for measurements relating to what is behind a wall. It is just a PITA and with no boxes and using rings it isn't as nice looking.
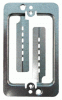
These work better but sort of fragile compared to a metal mudplate.
Personally here I used metal mud plates as mentioned previously pre dry wall and plastic rings post drywall. I wanted uniformity here with the electrical boxes such that every mud plate installed was totally even with the electrical boxes whether they were low or high. The metal mud ring here provided a solid base for me and it was already pre cut.
These were installed with no boxes or plastic boxes if necessary for speakers, wall keypads, network LV or whatever right after the electrician had installed his stuff.
I did want music and networking right away. Initially did use blanks and that was low on the WAF and a push to terminate these right away. The in wall speaker mud plates were totally removed and the in ceiling or wall speakers were larger that the mud plates and holes. I did bulk purchase these as I did in the Midwest by the case way back then.
So first LV setups related to speakers and keypad controls for the speakers then network / television all done up within a month or two. The alarm prewire had been done and here there was no rush to terminate these and the ends were capped such that you didn't see them. (doors and windows).